The optical fiber production process
FIND OUT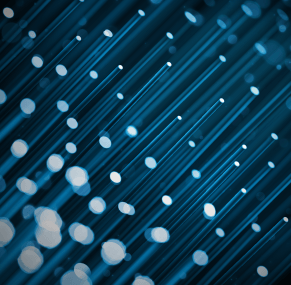
A glass preform for manufacturing optical fiber
Everything starts with silica sand. Highly purified materials are then combined to manufacture a glass cylinder, called a Preform: a multi-layered pure glass cylinder of around 20 centimeters in circumference . It is comprised of two perfectly concentric tubes, each with a different light refraction index. Several different horizontal processes (IVD, OVD, VAD) are used to manufacture the preform. The objective is the same: to provide the finished drawn fiber with the best performance properties possible. The preform is then mounted atop a tower and its base is heated in a furnace (ay more than 2,000°C) to produce a fine droplet that will fall by gravity and will be drawn down to obtain a narrow, uniform diameter of around 100 microns. High-purity, oxygen-free Argon gas is cycled through the furnace to protect the graphite components at such high temperatures. The core/clad ratio of the preform is maintained during the draw process. The resulting optical fiber has this same core/clad ratio. In fact, the preform is a large, solid version of a fiber.
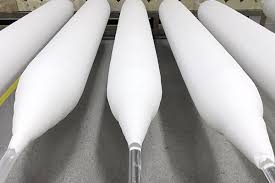
From the preform to the finished optical fiber.
During the process, the bare fiber is first cooled down to apply two layers of a coating material such as acrylate or polyimide that provide protection and bending properties. The temperature of the fiber needs to be reduced for proper coating application.A capstan at the bottom of the draw tower continuously pulls and winds up the glass fiber. The speed of the fiber draw depends on the preform, fiber type and available equipment. It may be a few meters per minute up to 4,000 meters per minute for cutting-edge telecommunication fiber production. The draw speed is carefully monitored to control the finished fiber diameter. All of the equipment involved must be concentric ally aligned in order to produce a perfectly round filament of glass. Optical fiber dimensions are directly dependent on this factor.
The drawing force applied on the fiber during drawing must be accurately controlled in order to optimize light propagation in the fiber. Several measuring devices located all along the drawing tower provide many data items to monitor final dimensions and the overall quality of the fiber.
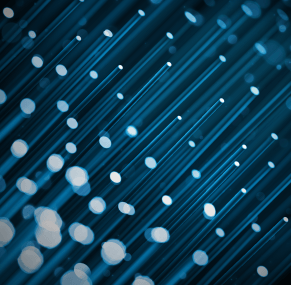
Sort and test of the final optical fiber
The finished optical fiber is wound onto spools with a capacity of several kilometers until the preform is used up. A number of mechanical tests are done on it to avoid any future risk of breakage. Then, smaller reels are used to sort and classify the optical fibers according to their future applications. Globally, we can differentiate the fiber into two categories: single-mode fiber (long distance usage) and multi-mode fiber (for shorter distances). Typically, the final diameter for both fibers is 250 µm. After drawing, optical fibers are tested to verify that all their other properties meet their specifications and customer requirements.

Our articles related
Contact the company CERSA MCI
Do you have a specific control and measurement need?
Are you looking for a high-performance control device?
You wish to request one of our services?